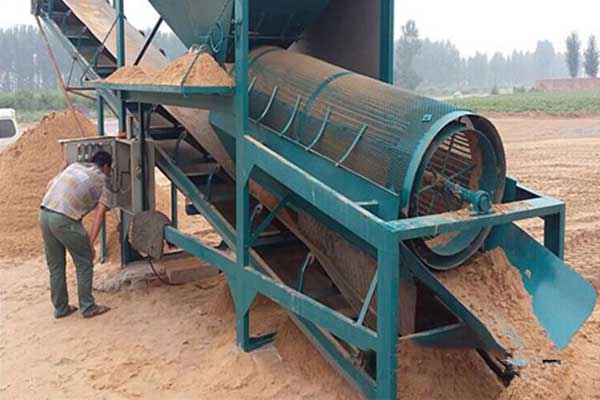
Dirt screeners play an essential role in separating debris, rocks, and unwanted materials from soil, helping you create a finer product for landscaping, gardening, or construction purposes. Whether you’re running a business or maintaining a large property, keeping your dirt screener in top condition is key to ensuring long-term efficiency and profitability. If you’re in the market for a dirt screener for sale, it’s crucial to understand how to maintain and operate it for optimal performance.
In this article, we’ll cover everything you need to know about maintaining and operating your dirt screener, including essential maintenance tasks, operational tips, and troubleshooting common issues.
What is a Dirt Screener?
A dirt screener, also known as a soil or aggregate screener, is a machine designed to separate soil from unwanted materials such as rocks, sticks, and debris. Dirt screeners are commonly used in construction, landscaping, and gardening to produce cleaner soil that can be reused or sold.
There are different types of dirt screeners available, ranging from small, portable models to large industrial machines. The primary function of a dirt screener is to pass the soil through a vibrating or rotating screen, leaving behind larger debris that can be discarded or repurposed.
Why Regular Maintenance Matters
Maintaining your dirt screener is crucial to extending its lifespan and ensuring that it operates efficiently. A well-maintained machine will:
- Reduce downtime: Regular maintenance prevents unexpected breakdowns and costly repairs.
- Improve productivity: A machine in top condition will process soil more efficiently, increasing the volume of clean soil produced.
- Extend lifespan: Proper care and maintenance can significantly extend the life of your dirt screener, protecting your investment.
- Enhance safety: Machines that are regularly inspected and maintained are less likely to malfunction, reducing the risk of accidents on the job site.
Daily Maintenance Tips for Your Dirt Screener
Daily maintenance routines are essential for keeping your dirt screener in optimal working condition. Before and after each use, follow these steps:
1. Inspect the Screener
- Check for any signs of wear or damage to the screen, frame, and other components.
- Ensure that there are no loose bolts or connections that could cause malfunction during operation.
2. Clean the Screen
- After each use, clean the screen to prevent the buildup of dirt, rocks, and debris, which could clog the machine or reduce its effectiveness.
- Use a brush or air compressor to clear any trapped materials from the screen.
3. Lubricate Moving Parts
- Regularly lubricate moving parts, such as bearings and joints, to ensure smooth operation.
- Follow the manufacturer’s guidelines for the type and frequency of lubrication.
4. Check Hydraulic and Oil Levels
- If your dirt screener operates using hydraulic components, check the hydraulic fluid levels daily.
- Inspect oil levels and ensure there are no leaks that could cause damage or performance issues.
5. Inspect the Power Source
- If your dirt screener is powered by an engine, check fuel levels, oil, and other fluids to ensure smooth operation.
- Clean air filters and inspect belts for wear and tear.
Weekly Maintenance Routines
In addition to daily tasks, weekly maintenance should include more in-depth inspections and tune-ups to keep your dirt screener in optimal shape.
1. Check for Wear and Tear
- Examine the screen for any damage, such as tears or holes, that could affect performance.
- Inspect the frame and support structures for signs of rust or fatigue, particularly if the screener is used in harsh environments.
2. Tighten All Bolts and Fasteners
- Over time, vibrations from the machine’s operation can loosen bolts and fasteners. Make sure everything is securely tightened to prevent structural damage or accidents.
3. Inspect Belts and Pulleys
- Check all belts and pulleys for signs of wear. Replace any parts that show significant deterioration to prevent breakdowns.
4. Replace Worn Parts
- Any components showing significant wear should be replaced immediately to avoid compromising the entire machine. This includes screens, bearings, or hydraulic components.
5. Inspect Electrical Components
- If your dirt screener uses an electric motor, inspect wiring and connections for any signs of damage or corrosion. Replace worn parts as needed.
Operational Tips for Optimal Performance
Operating your dirt screener correctly will not only improve the quality of your soil but also prolong the life of the machine.
1. Choose the Right Screen Size
- Select the appropriate screen size based on the type of soil and the materials you need to filter out. A finer screen will filter smaller debris, while a coarser screen is ideal for separating larger rocks and stones.
2. Avoid Overloading the Screener
- Never exceed the recommended load capacity for your dirt screener. Overloading can cause damage to the machine and reduce its efficiency.
3. Feed Soil Evenly
- To ensure smooth operation and even filtration, feed the soil into the screener at a steady pace. Avoid dumping large loads at once, as this can overwhelm the screen and lead to clogging.
4. Monitor Vibrations
- Watch for any unusual vibrations during operation, as this could indicate a problem with the machine. Address any issues immediately to prevent further damage.
Common Issues and Troubleshooting
Even with regular maintenance, dirt screeners can encounter issues. Here are some common problems and their solutions:
1. Clogged Screen
- Solution: Clean the screen regularly and avoid overloading the machine to prevent clogs.
2. Machine Vibrating Excessively
- Solution: Check for loose bolts or fasteners, and inspect the bearings for wear. If necessary, replace worn parts.
3. Hydraulic Leaks
- Solution: Inspect hydraulic hoses and seals for any signs of leakage. Replace damaged components and refill hydraulic fluid as needed.
4. Engine Issues
- Solution: For gas-powered screeners, inspect the fuel system, air filters, and spark plugs regularly. Ensure that the engine is well-maintained and serviced as per the manufacturer’s guidelines.
Dirt Screener for Sale: What to Look for in a New Unit
If you’re searching for a dirt screener for sale, it’s essential to know what features to look for to ensure you’re getting the best value for your investment.
1. Screen Size and Capacity
- Choose a dirt screener with a screen size that suits your needs. Larger screeners may be more efficient for commercial use, while smaller models are better for personal or small business applications.
2. Portability
- If you need to move the screener between job sites, look for a model with portability features such as wheels or a trailer hitch.
3. Power Source
- Decide whether you need a gas-powered, electric, or hydraulic dirt screener, depending on your job site’s requirements.
4. Durability
- Look for durable construction materials such as heavy-duty steel frames and corrosion-resistant components to ensure the screener can withstand tough conditions.
5. Warranty and Support
- Ensure the screener comes with a solid warranty and access to customer support, so you have peace of mind if any issues arise.
Conclusion
Maintaining and operating your dirt screener is essential for maximizing its performance and longevity. By following daily and weekly maintenance routines, as well as adopting best practices during operation, you can ensure your screener remains in top condition. If you’re in the market for a dirt screener for sale, make sure to choose a model that fits your specific needs, whether you’re using it for commercial purposes or home projects.