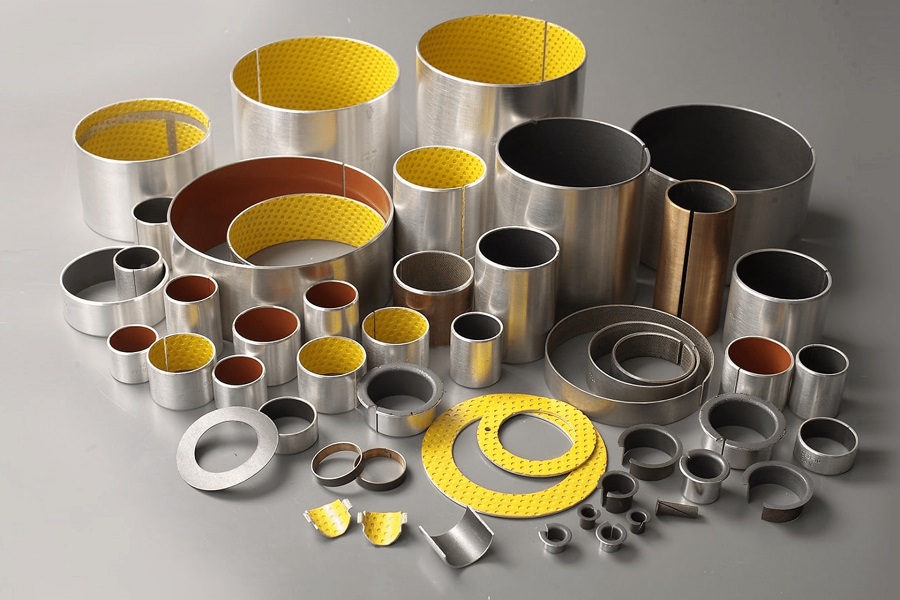
Renewable energy is critical to meeting global electricity demands sustainably. As the world transitions to clean power, innovations in wind turbine technology will be crucial to unlocking wind energy’s full potential.
The Importance of Scale in Wind Turbine Design
Bigger wind turbines can capture exponentially more energy, creating superior economics. The average commercial turbine size has surged over the last decade. Today’s offshore turbines stand over 850 feet tall with more than 600-foot diameter rotors.
But gigantic scales create immense engineering challenges. Major components must withstand tremendous structural loads over 20+ year lifetimes. Critical drivetrain elements connecting rotors to generators experience extreme dynamic stresses. Maintaining such massive machines operating offshore is vastly more difficult.
This is where custom carbon graphite bushings provide unique solutions for oversized main bearings, pitch systems, and other applications in cutting-edge wind turbines.
Custom Carbon Bushings Optimize Main Rotor Bearings
Main rotor bearings support the entire weight of wind turbine nacelles and rotors. They experience radical radial or axial loads, making their wear resistance and stability vital. However, the raw scale of bearings needed for multi-megawatt turbines pushes traditional bearing materials like metal alloys to their limits.
Carbon graphite offers superior properties:
- Extreme strength yet lightweight to minimize loads
- Excellent thermal conductivity to dissipate heat
- Low friction coefficients to reduce wear
- Self-lubricating without auxiliary lubricants
- Resilient in offshore environments
Custom bushing solutions let engineers tailor carbon or graphite to the exacting demands of high-capacity main bearings. Proprietary impregnation processes optimize bearings for load capacity, temperature stability, friction characteristics, and more.
Enhancing Pitch Control Reliability
Hydraulic rotor blade pitch control systems adjust blade angles to regulate turbine power output. However, actuating the immense aerodynamic forces requires these systems to pitch blades longer than football fields, creating extreme bearing or bushing loads.
Custom carbon or graphite bushings shine here. Their unparalleled strength, low friction, and dimensional stability across temperature changes improve pitch control reliability on high-output wind turbines. Custom bushings withstand tremendous hydraulic pressures and cyclic loads over numerous pitch adjustments without failure.
The importance of advanced materials cannot be overstated. The development of custom carbon or graphite bushings is just one example of how innovation can solve complex engineering challenges and push the boundaries of renewable energy technology.
As the world strives for sustainable solutions, these advancements are not just technological breakthroughs. They are key players in ensuring the reliability and efficiency of wind turbines, thereby supporting global efforts to transition to cleaner energy sources.
Boosting Lifetime Reliability
The reliability of wind turbines over 20+ years of operating lifetimes is paramount. Custom carbon or graphite bushings enhance reliability in multiple ways:
Exceptional Wear Resistance: Carbon or graphite’s low friction coefficients drastically cut component wear even under extreme loads. This reduces maintenance needs and prevents unexpected failures.
Thermal Stability: Custom bushings maintain critical tolerances across temperature fluctuations offshore. This prevents binding or seizing issues and ensures smooth operation.
Corrosion Resistance: It resists corrosion in salty, humid ocean environments. Metal bearings require extensive protection to avoid corrosion-related failures.
Driving Down Lifecycle Costs
Carbon or graphite bushings also reduce costs over lengthy wind turbine lifecycles:
Lower Maintenance Requirements: Custom bushings’ self-lubricating properties and wear resistance slash maintenance needs. Less frequent replacement or refurbishment generates substantial long-term savings.
Improved Capacity Factors: Carbon bushings boost reliability and minimize unexpected downtime, maximizing energy output and capacity factors—critical drivers of wind farm profitability.
Lightweight Design: Carbon materials’ low density enables lightweight components that cut nacelle weights, reducing tower costs and logistical complexity.
Unlocking Revolutionary Design Flexibility
Carbon or graphite bushings empower revolutionary mechanical designs far exceeding the limits of metal bearings:
One-Piece Construction: Monolithic carbon bushings operate without joints, removing failure points. This enables enormously scaled-up single-piece main rotor bearings.
Geometric Freedom: Carbon materials can be formed into complex free-form geometries optimal for load distribution, unlocking innovative bearing designs.
Embedded Sensors: Strain gauges and sensors can be incorporated directly inside carbon bushings for condition monitoring. This predictive maintenance capability boosts uptime.
Accelerating the Sustainable Energy Transition
Growing wind power is pivotal to the global energy transition and emissions reductions. Innovations like custom carbon graphite bushings will accelerate the adoption of clean, renewable wind energy.
As turbines rapidly scale up, carbon or graphite solutions empower engineers to push boundaries in mechanical design. No other bearing material matches the exceptional strength, low friction, and fabrication flexibility needed in high-capacity 21st-century wind turbines.
Ultimately, these technologies will enable massively scaled wind power to sustainably supply over 50% of global electricity. The future of ultra-low-cost, ultra-reliable wind energy depends on innovations in custom carbon or graphite bushings at the drivetrain level.